Re-thinking the Recycling of Plastics through Materials Regeneration.
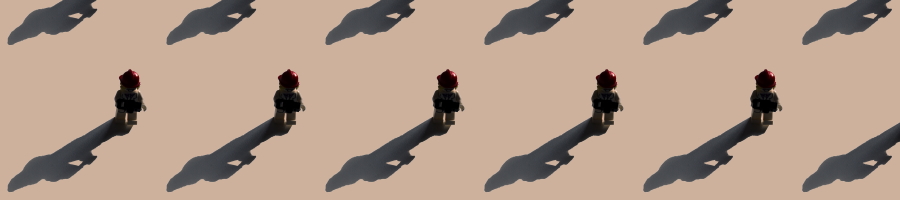
We are facing a global plastic waste crisis that affects all ecosystems, polluting water and soil, harming wildlife, and threatening communities that depend on healthy ocean and river environments. Most commonly used plastics are neither recycled or capable of biodegradation, but rather are either sent to a landfill or burned, or worse end up in the natural environment. Consumers and companies can play a role in changing this negative trend, for example by reducing their use of single-use plastics, or by recycling, but we need an entirely new paradigm if we are really going to address this problem at a global scale. One direction has to be use less virgin plastic by significantly increasing the recycled content of all plastics, while another option is to make biodegradable plastics that can return to CO2 and biomass within the environment. However, plastic recycling currently presents several major hurdles both from a technological and economic point of view, and biodegradable plastics are not in common use, due to cost and availability.
Traditional plastic recycling involves melting and recasting of thermo-plastics, one of the most common example being PET from plastic water bottles recycled into polyester fibers. During use, all plastics physically degrade and become contaminated with foreign substances, and because of this, recycled plastic products generally contain only a small amount of recycled material - A 100% “recyclable” plastic product usually contains less than 20% recycled material!
At the Center for Renewable Materials, we focus on developing new plastic based materials – derived from renewable resources and designed to biodegrade or be recycled at the end of life. In particular, we have developed bio-based polyester polyols made from renewable algae feedstocks that, when combined with isocyanates, have been used to make a variety of polyurethane (PU) foams, elastomers, coatings, and adhesives, all of which have been shown to meet commercial specifications. These materials have also been shown to be biodegradable under a variety of environmental conditions, and we have identified both the biodegrading organisms as well as their secreted enzymes - that can be used to enzymatically return these polymers back into their starting monomers. In addition, we have developed polyester thermoplastics, including polyester fibers and films, that can be biodegraded within the natural environments. This is the simplest sustainable scenario, with a complex material degrading in components not harmful for the environment at the end-of-use of a product.
In collaboration with key industrial partners, we are developing a process for the enzymatic depolymerization and recovery of monomers from bio-based polyester and polyurethane products, that will result in a new approach to plastic recycling. We use the recovered monomers to prepare new products that meet commercial specifications, demonstrating a viable circular carbon economy for these products. We call this process “Bio-Loop”. Rather than melting the plastic for recasting, under Bio-Loop the polymer is depolymerized back to starting raw materials that are then recovered and used as feedstock for creating new monomers. This depolymerization process follows the exact same mechanisms as biodegradation, except that rather than have the depolymerized monomers metabolized by microorganism back into CO2, we capture those monomers and reuse them to make new materials. During this depolymerization and recovery process, damaged monomers are separated from intact ones, and contaminating materials are also removed. Hence, we can produce new monomers from regenerated raw materials that can contain up to 100% recycled materials - without significant loss of quality. The biodegradability of the product is preserved at any stage of the Bio-Loop, so should one of our products end up in the environment, rather than back to us to be recycled, that product will simply biodegrade wherever it may be.